moteus cooling fans
mjbots.com now stocks PWM controlled cooling fans with RPM sense and mounting brackets that are compatible with the moteus-r4, moteus-n1, and moteus-x1. Check them out here:
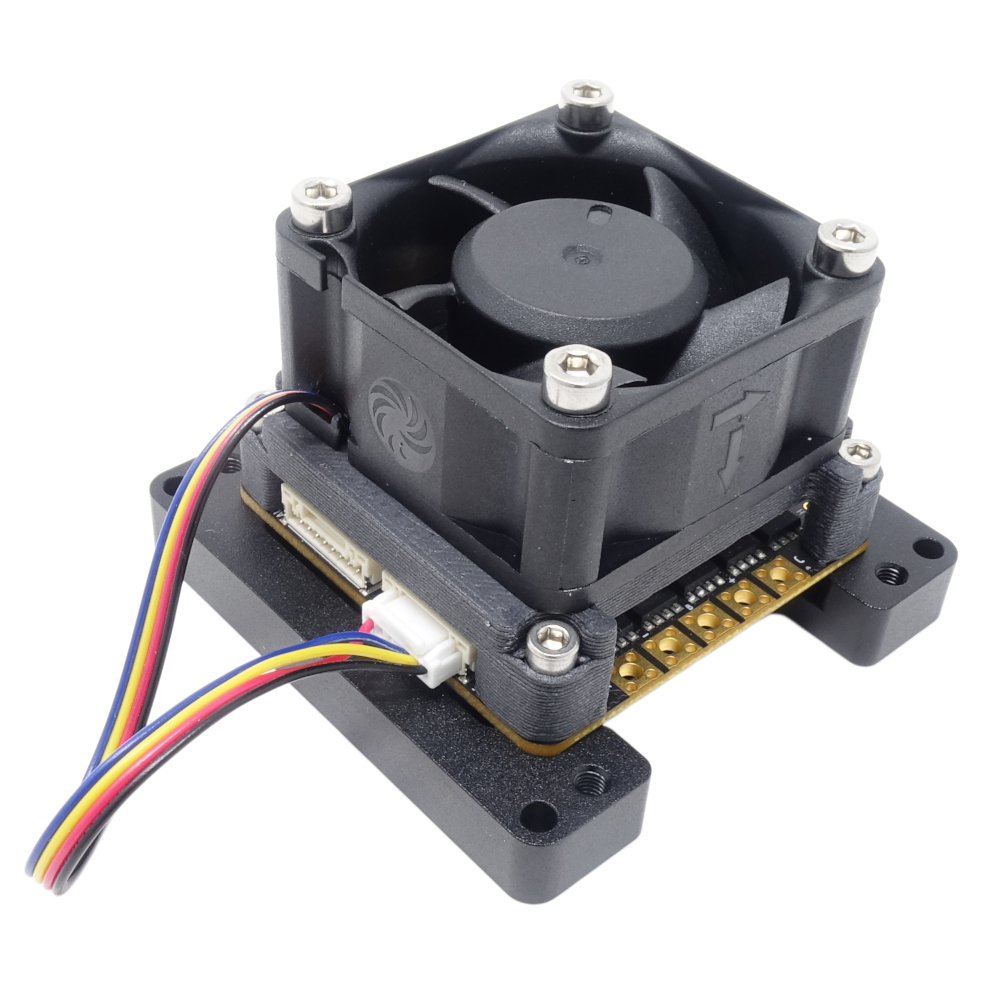
GH7 fan on moteus-n1 with mount
Read on to see how much these can improve the performance of your system and what configuration options are available.